
Tech development convergence making manufacturing IoT practical
By Max BurkhalterSeptember 20, 2019
The concept behind the industrial internet of things is clear in manufacturing. Companies that have more access to data on the factory floor will be able to make more informed decisions. This better real-time view of processes will help supervisors boost efficiency, maximize maintenance effectiveness and deliver generally smoother operational procedures.
The challenge associated with achieving such improvements comes from the fact that, in many cases, the machinery present in today's manufacturing settings is not yet enabled with the sensors that will create IIoT conditions. Organizations will have to make concerted and strategic investments in future-minded tech tools to collect, process and use real-time data from their factory floors.
In recent years, with technological development constantly ongoing, this process of improving IT in industrial settings has become easier and more affordable. Companies that previously considered themselves unable to commit to the IIoT may find conditions have changed enough to make the investment. Eventually, businesses that don't implement such intelligent features in their manufacturing supply chains may become the exception, and they run the risk of falling behind their competitors.
IIoT evolution expands
Medical Device and Diagnostic Review recently spoke with MachineMetrics Chief Data Scientist Lou Zhang about the rise of IIoT enablement in manufacturing environments. Conceding that many machine shops are still working on data-poor models that haven't changed in decades, Zhang suggested that change is on the way due to the fact that recent tech developments are pointing toward pervasive IIoT use.
The current state of the manufacturing industry, according to Zhang, is hampered by its lack of visibility. He noted that individual machine operators are often the only people in a facility who know exactly what each piece of equipment is producing hourly. The exact status of assets isn't being tracked in real time, leading to the same level of transparency that was possible in the early 20th century, but little more.
The development of new sensor hardware that is affordable enough to deploy en masse has made the outdated manufacturing model unnecessary, Zhang told Medical Device and Diagnostic Review. Of course, collecting data is not valuable if there is no way for companies to effectively route and analyze that content. Fortunately, functionality increases and price drops have come to other important elements of the network.
Zhang highlighted edge devices as pivotal components. These computing devices are stationed on the factory floor and act as the hub that collects information from connected machinery. Manufacturers are able to buy these hubs for as little as $500, making the investment in IIoT enablement much easier to square than it was in the days when the components cost thousands of dollars.
The software component of IIoT has similarly decreased in pricing and complexity, largely thanks to the cloud. Zhang cited Amazon Web Services-based applications as emblematic of the new manufacturing IoT paradigm. Companies can now gain access to the computing power they need for real-time monitoring, analytics and other valuable data management processes. Now, with access to more data than ever and ways to use it, companies are able to boost their efficiency in ways they couldn't only a few years ago.
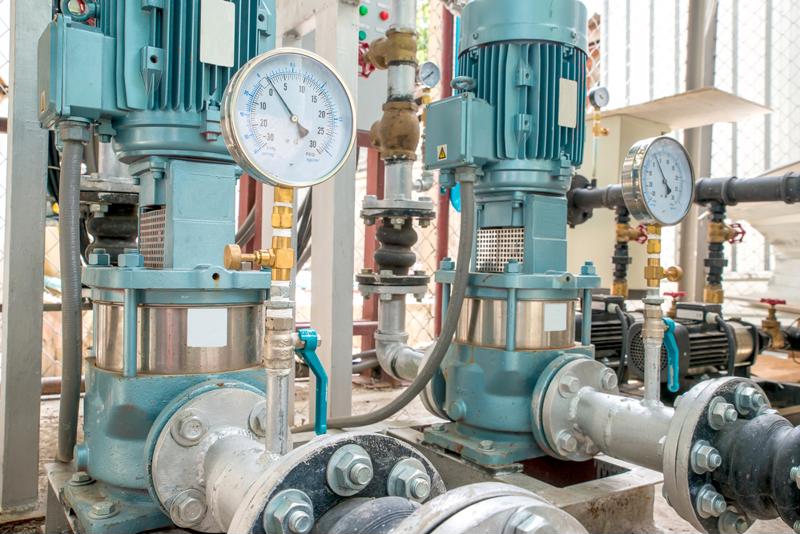
Use cases become clear
Embedded Computing Design contributor Lou Lutotanski recently laid out the path industrial companies are taking, bolstered by their new technological tools. Once these businesses have IoT sensors in place, for example, it becomes easier for them to automate greater portions of the manufacturing process. With predictive analytics enabled by real-time data capture from sensors, these companies can make their automated processes more effective and efficient. Rather than just making machinery run the same way at all times, these systems can react predictively.
Businesses are boosting their safety thanks to their increased IoT frameworks, according to Lutotanksi. The same sensors that allow organizations to track the status and speed of a piece of equipment can also detect unsafe conditions and trigger automatic failsafe and shutdown processes. Machinery that is overheating or otherwise malfunctioning may turn of automatically, or at least alert employees of its status, enabling a swift response.
Lutotanski added that rather than companies having one path to extract value from an IoT upgrade, they can get return on investment in several interconnected ways. From improving remote monitoring and servicing of factory floor assets to analyzing equipment usage and integrating real-time data with centralized databases, there are numerous processes improvements available with IoT infrastructure. Considering the falling prices of the necessary components, the time appears right to pursue these advantages.
Industrial automation will depend on reliable hardware such as Ethernet switches and serial to Ethernet converters. Check out some of the ways Perle has enabled industrial clients to reach their technological potential.