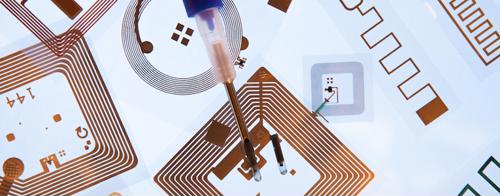
Recent advances in sensing technology push Industry 4.0 forward
By Max BurkhalterOctober 23, 2019
Smart technologies have become indispensable to companies across the industrial sector, offering enhanced visibility over critical assets, improved decision making and greater data collection capabilities than ever before. In a sense, the modern industrial era is characterized by big data and automated systems, but the rapid pace of technological innovation has left some organizations behind. One issue is that it can be difficult and costly to integrate smart tech into the legacy systems used by many manufacturing, agriculture, construction and other industrial players. To truly modernize, companies often need to rebuild their physical and digital infrastructures with an eye for instantaneous connectivity and data sharing, while also keeping their systems scalable to accommodate future advancements.
Finding the perfect balance between analog and digital-centric processes is no easy task, especially considering how disruptive large-scale deployments can be. This, in part, has led to a surge of interest in adaptable smart technologies that can be attached to legacy machinery without prolonged downtime, such as environmental sensors. According to estimates from Allied Market Research, the global sensor market is expected to reach $287,002 million by 2025 - but to understand why these devices are so valuable in industrial settings it's important to review how they fit into the bigger picture.
Industry 4.0 and the power of information
Over the past few years, technology experts across the industrial sector have been speaking at length about "Industry 4.0", though many seem to operate from different definitions. According to Deloitte, Industry 4.0 "marries advanced manufacturing techniques with the Internet of Things to create manufacturing systems that are not only interconnected, but communicate, analyze, and use information to drive further intelligent action back in the physical world." Of course, the effectiveness of these interconnected systems is wholly dependent on the precision of the data collected by embedded sensors - a single faulty sensor can generate a host of cascading inaccuracies that may lead to poor asset management decisions.

Whether an organization chooses to embrace wireless IoT sensors or stick with their hard-wired counterparts is, for the time being, of little consequence. Both options offer enhanced visibility over production environments and worksites, while also being relatively easy to install. Companies looking to improve their data gathering capabilities can outfit everything from heavy machinery and HVAC equipment to work vehicles and even employees with sensing technologies. This enables management teams to closely monitor productivity and make informed improvements over time. That said, modern sensor technologies aren't without their shortcomings.
As pointed out by Ed Sappin, Forbes contributor and CEO of Sappin Global Strategies, today's commercial IoT sensors currently face two operational hurdles: system integration and long-term performance. The issue is that most industrial settings require sensors that can operate reliably in harsh conditions. For example, manufacturing equipment often runs at high temperatures and can generate intense vibrations, both of which can reduce the lifespan of even the most resilient sensors. What's more, production environments that utilize corrosive chemicals must take extra precautions to insulate their smart tech from serious physical damage.
In terms of functionality, many of the industrial sensors on the market are only able to monitor a single environmental factor, whether it be temperature, sound, light or vibrations. This lack of versatility may force manufacturers and organizations in other industrial settings to install several sensors on each piece of equipment, introducing multiple points of failure into their network of IoT devices. Luckily, recent advancements in sensing technology may hold the key to overcoming these and other limitations.
The future of sensing technology
Ultimately, the success of Industry 4.0 relies on the continued advancement of sensing technologies, particularly in the initial data measurement phase. Sensors that are able to collect precise information in large quantities are only growing in demand, in part due to the increasing sophistication of artificial intelligence and data analysis software. One promising development in smart sensing equipment is the incorporation of nanomaterials. According to Mouser Electronics, the small size of nanomaterials like graphene can provide a larger surface area for detecting fluctuations in the environment, making them well-suited to sensitive equipment.
Although these types of "nanosensors" are still under development, they have already attracted the attention of many professionals in the communication and medical industries. For one, the small scale of these devices make them ideal for measuring changes in the human body, allowing doctors to track a patient's exact condition in real time. Like most innovations in IoT, the progress made by one commercial industry (whether it be the medical or communication field) will increase the viability of nanomaterial sensors across the board. However, implementing a large-scale system of this nature requires a lot of planning and investment in infrastructure.
Perle offers powerful networking tools that can help increase production efficiency and facilitate stable data networks, like our reliable ethernet extenders and industrial-grade terminal servers. Read some of our customer stories to find out how we've empowered other industries to embrace Industry 4.0 initiatives.