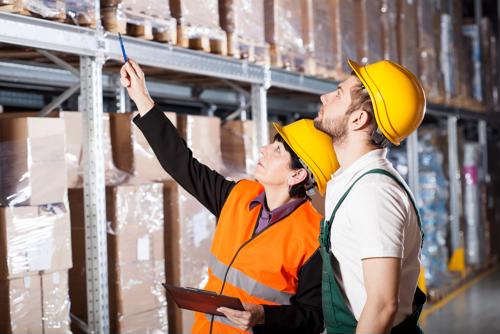
Quality control in the era of IoT and automation
By Max BurkhalterAugust 20, 2020
Quality control is fundamental to every industry that designs, produces or transports physical goods, but is particularly important in manufacturing. As the software developer BehrTech explains, manufacturers strive for consistent, high-quality results and minimal rejection rates to help offset the volatile market demand and steep material costs that are the norm in the industry. When paired with the "mission-critical nature" of end products, it's no surprise that many manufacturing firms have been hyper-focused on improving their quality control processes and integrating new technologies to give them a competitive advantage.
In today's tech-centric landscape, the ability to monitor and control production equipment is paramount to the quality of manufactured goods. Technicians are constantly recalibrating equipment and optimizing production lines to ensure consistent process parameters and eliminate time-wasting inefficiencies. The same retooling is also taking place in the later stages of production, with automated systems and robotics playing a key role. Historically, manufacturing plants employed workforces of trained quality assurance specialists to verify the integrity of finished goods. But with the rise of internet-of-things technologies and Industry 4.0, companies are integrating new processes and systems to streamline product monitoring and flaw detection tasks.
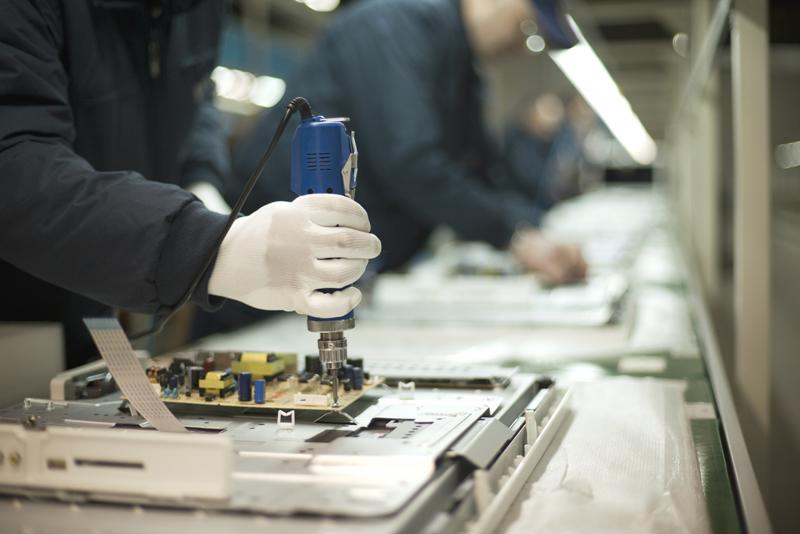
How IoT is impacting quality control
For manufacturers, IoT technologies represent the next step in real-time monitoring, process automation and data analytics. By outfitting production lines with dozens of IoT sensors, plant managers can keep track of environmental conditions, equipment performance and more. This added insight can allow manufacturers to better understand where quality control issues stem from, and take action with renewed confidence. In terms of specific applications, IoT is helping manufacturing companies:
- Perform predictive maintenance: Instead of waiting for a piece of machinery to fail, manufacturers are using IoT sensors to help forecast when certain internal components will break down. As senior director of reliability engineering for Cushman & Wakefield, David Auton, explained in an interview with Buildings.com, "run to fail or repair easily costs somewhere between three and 10 times as much as a good maintenance program." This is without considering the productivity losses that can result from unplanned downtime. Equipment maintenance also has an impact on quality control, as uncalibrated machinery can introduce flaws and irregularities in finished products. By remaining proactive about maintenance and repair, manufacturers can simultaneously lower their overhead costs and reduce rejection rates.
- Monitor production remotely: Another benefit of IoT systems is that they can be monitored and controlled by off-site employees. This capability is especially important in the current business climate, where the COVID-19 pandemic has forced companies to curtail their physical operations. Using vision inspection systems, manufacturers can continue to perform key quality control tasks without the need for manual intervention. For example, thanks to recent innovations from Sightline Process Control Inc., bakeries around the world are able to integrate high-speed visual measurement tools into their workflows, AZO Materials reported. These systems are able to analyze up to 100 objects per second, helping identify defective baked goods before they're sent out to customers.
- Automate production processes: Once a manufacturing plant is outfitted with IoT sensors, worksite managers can begin integrating robotic process automation and other technologies to help make their operations more reliable. The massive amount of data these sensors collect can be fed into a machine-learning algorithm or an AI-powered platform to help drive real-time insights. In a fully networked manufacturing environment — one that is equipped with machine-to-machine communications — automated systems can detect output variations and send that data to downstream equipment. This can allow the equipment itself to make minor adjustments on the fly, including those that impact product quality.
While quality control is a major priority for manufacturing firms, IoT can also provide enormous benefits in terms of innovation and process development. Armed with environmental data and performance analytics, plant managers can locate inefficiencies and oversights that waste time and money. These findings can empower manufacturers to improve subpar processes, create more efficient material handling strategies and ensure consistent outputs across multiple production sites. This partially accounts for why more than 40% of all active IoT devices will be used in industry and manufacturing over the next 10 years, according to research from Intel. Of course, to prepare for Industry 4.0 and the quality control revolution currently making waves in the manufacturing industry, companies will need to have the right networking equipment in place.
Perle offers industrial-grade connectivity tools that are designed for use in the harshest conditions, including indoor manufacturing plants and outdoor installations. Our industrial media converters and Ethernet switches are built to exceed commercial specifications, making them ideal for big data environments with high ambient temperatures.
To learn more, read some of our customers' success stories.