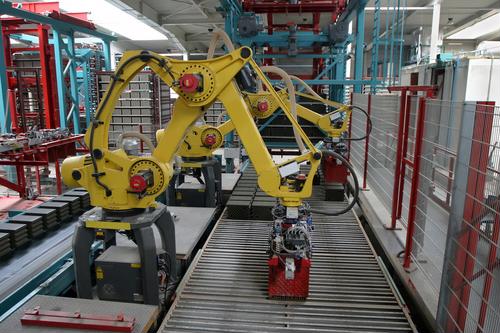
Predictive Maintenance Improve Industrial KPIs
By Max BurkhalterOctober 12, 2022
The Internet of Things (IoT) is the network of physical objects that are embedded with electronics, software, sensors and connectivity to enable these objects to collect and exchange data. Industrial machinery is being transformed by the IoT revolution. This technology has been integrated into manufacturing to make production more efficient and sustainable. It has also made it possible for machines to communicate with each other and make decisions on their own without human intervention.
IoT has the potential to have a continued major impact on industrial machinery over the next few years. There are a number of factors that will determine how successful IoT will be in industrial machinery. These include the level of interest in IoT among industrial machine manufacturers, government regulations on data privacy and the availability of suitable technologies for IoT-connected machinery. One major growth in the industry is the continued use of predictive maintenance.
What is predictive maintenance?
Predictive maintenance is a process that involves collecting data about equipment, structure and facilities and then using that information to predict the potential for failure. By doing this, organizations can improve their KPIs, reduce downtime, boost operational efficiency and increase revenue and profits. Prediction of failures allows for proactive maintenance that can prevent downtime from occurring in the first place.
Customer satisfaction also increases through the use of predictive maintenance by establishing more efficient operations, which leads to better retention rates. Furthermore, predictive maintenance can minimize injuries by ensuring that machines are kept in good working condition and help to optimize operations by ensuring that there is always enough stock on hand.
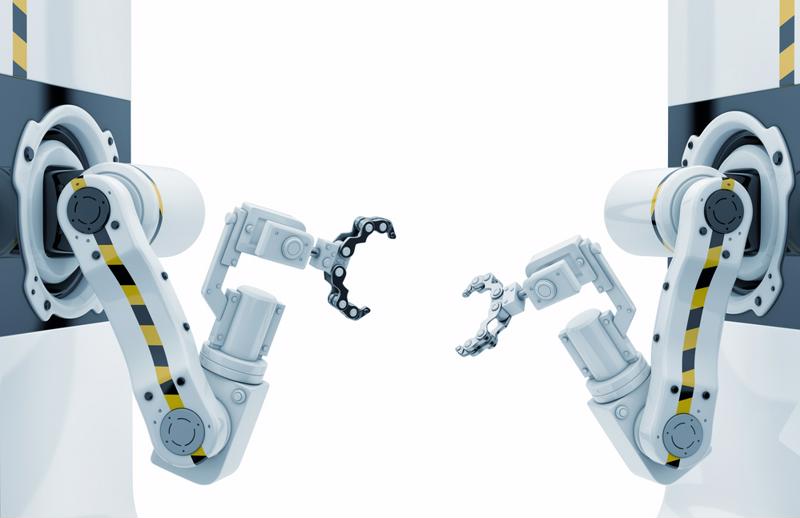
How does predictive maintenance work?
The science behind predictive maintenance is a combination of different technologies including sensors, data analytics and machine learning. The predictive maintenance system has two parts: the monitoring system and the prediction model. The monitoring system collects sensor data from equipment that needs to be monitored. The prediction model predicts when the equipment will fail based on past performance and sensor input data.
It's essentially a philosophy that tries to anticipate the future needs of a product and plan for them before they become a problem and also attempts to predict failure by using data from previous product failures. This data can be collected from historical records such as maintenance logs, inspection reports and warranty claims.
Data from predictive maintenance infrastructure can also be collected through simulation models that estimate future product life cycles. These models can be based on factors such as past experience, design complexity and process variables. These models are used to predict when parts will wear out or fail. If predictive maintenance is used in conjunction with preventive maintenance this can help prevent failure by acting as a guard against potential issues. Using predictive maintenance can also reduce the overall cost of maintaining products since it can allow companies to repair or replace parts sooner than they would have otherwise.
Perle leading the way in industrial technology adaptation.
Perle systems remain at the forefront of increased efficiency assistance tools for the industrial industry. Our case studies showcases the variety of enterprises that have benefited from Perle industrial switches and console servers.