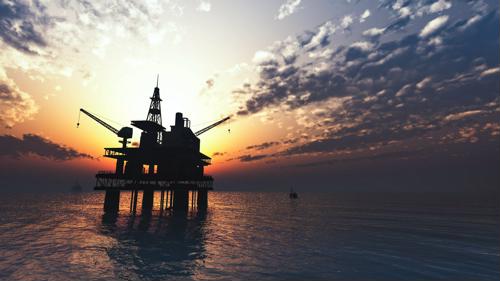
Oil and gas companies address worker deaths, spills with connected technology
By Max BurkhalterMarch 16, 2017
Professional journeyman Edwin Drake debuted the first functioning petroleum-drilling rig Aug. 27, 1859 in Titusville, Pennsylvania, according to Time magazine. Drake used the device to bore almost 70 feet beneath the surface, accessing the first domestic oil deposit and catalyzing an energy revolution. In the decades since, the oil and gas sector has experienced astronomical growth. However, the job of collecting, refining and transporting petroleum hasn't gotten easier since Drake established his wood-cladded well.
A new generation of connected energy technology has the potential to spur progress by simplifying key production workflows and improving worker safety.
Drones perform dangerous duties
Oil inspectors perform essential, yet potentially deadly duties. Those assigned to offshore drilling rigs dangle from multistory platforms, searching for structural vulnerabilities that could hamper production or create safety hazards, Bloomberg reported. Others inspect inland storage tanks that emanate toxic gases that can cause asphyxiation or heart failure, according to The Wall Street Journal. While most manage to withstand these rough conditions, some sustain serious injuries or worse. In fact, the workplace fatality rate for oil workers is seven times greater than figures for professionals in other sectors, according to the Occupational Safety Health Administration. Consequently, many energy companies are searching for alternatives that might reduce risks. A few innovative firms have turned to drone technology.
Major oil and gas players such as Apache, BP and Shell collaborate with the London-based industrial drone maker SkyFutures, Bloomberg reported. The enterprise designs and builds customized unmanned aerial vehicles for use in the energy arena. Each device comes equipped with onboard processors and sensors that can create 3-D rig models, complete with mapped physical abnormalities that could indicate structural degradation. Plus, the drones can complete the task in far less time than rig workers.
"What we can capture in five days using a drone could take eight weeks with human inspectors," Chris Blackford, chief operations officer for SkyFutures, explained. "We can even inspect the flare stacks while in production, which saves money."
These massive fixtures power mission-critical drilling tools and shutting one down for an inspection can cost millions of dollars.
Oil and gas companies are also deploying drones on land, specifically in oil fields and pipeline systems. In 2015, General Electric launched the Raven quadcopter, which can access hard-to-reach spaces and detect pipeline damage. The company manages the project out of a research and development facility in Oklahoma City, according to Offshore magazine. Here, engineers perfect the Raven's emission-sensing capabilities. Currently, the vehicle can fly for 40 minutes and leverages laser-equipped sensors to collect readings. An operator can control its every move via a tablet computer.
The Raven accelerates the inspection process considerably, allowing oil and gas personnel to conduct full reviews three times faster than before.
"When you think of Project Raven and the usage of new tools and applications, it's going to be key to take the industry forward," Lorenzo Simoneli, CEO for GE, told Bloomberg. "There's a lot that you can do going forward to help drive productivity."
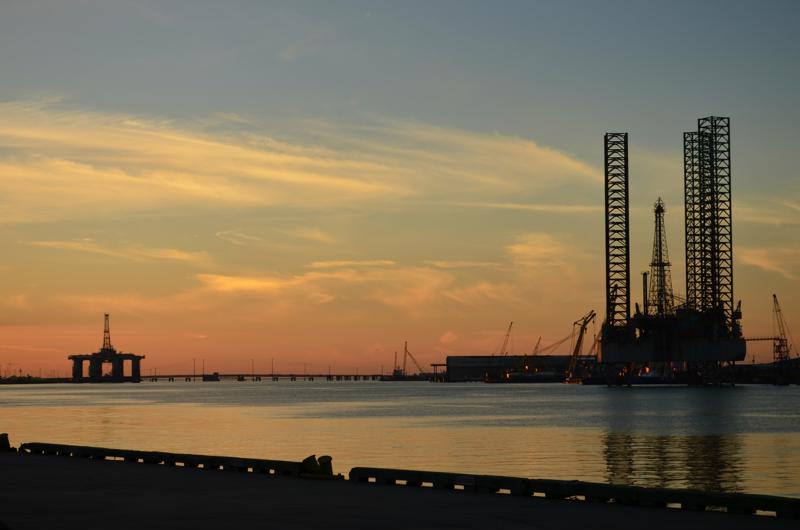
Deploying the pigs
In addition to monitoring easy-to-access petroleum production and delivery features, oil and gas organizations must also keep watch over more elusive components, such as pipeline interiors. More than 160,000 miles of crude oil line cover the U.S., according to data from the Department of Transportation. The businesses in charge of these vessels continually review them, searching for developing damage that could cause spills. Corrosion is the central culprit, building up on the inside of pipe walls and eventually eating through. Of course, tracking rust with human crews is no easy task and leaves room for error.
This is why many energy firms have begun using automated robots to patrol lines, Wired reported. These devices, called smart pigs, are covered in sensors and designed to navigate pipelines as oil flows. This allows for the collection of detailed oil line data and eliminates the need for full pipeline maintenance shutdowns, which prove costly. Most models use magnets and ultrasound technology to pinpoint line flaws and feature flexible chassis that can easily fit through telescoping tubes.
Surprisingly, smart pigs have been around since the 1960s, NPR reported. However, with the rise of connected technology, these tools have become more advanced and are now apart of most corrosion detection and prevention programs. Why? Their ability to gather large amounts of data.
"The amount of data recorded by one of these smart pigs is enormous," Al Crouch, an engineer and program director at the Southwest Research Institute in San Antonio, told NPR. "It's every square inch of a pipe for 100 miles or more, and all of that has to be stored on board the pig."
"Smart pigs use magnets and ultrasound technology to pinpoint oil line flaws and feature flexible chassis that can easily fit through telescoping tubes."
Even so, smart pig makers continue to improve their products, as the devices can pose problems. Some sections of pipeline are unpiggable due to extreme angles. Additionally, some devices have been known to malfunction, The Wall Street Journal reported. For example, cracks that run along pipe welds can evade pig sensors. One company is moving the smart pig forward, adding features that address this issue, along with others.
The Russian technology firm Diakont debuted a "form-fitting" smart pig back in 2015 that can handle extreme angles, move against petroleum torrents and scan literally uncharted pipeline, Motherboard reported.
"The problem is that you're not in control of where you are in the pipe," Brian Carlson, director of pipeline services for Diakont, told the publication. "If you see an anomaly, you're essentially just flying past it. Our system is very deliberate in the way it drives through the pipe, so you can stop and analyze anything as you're going through."
With these advanced pigs in play, the oil and gas industry is sure to see real improvements in line-scanning technology, across the board. These devices, together with inspection drones, have the potential to transform the sector, allowing energy companies to do away with everyday processes that have far too much in common with used during the initial stages of American oil boom.
Here at Perle, we provide the connective foundation needed to support drones, smart pigs and the other advanced technologies taking hold within the oil and gas sector. Perle device servers, terminal servers and fiber media converters help major organizations like Shell and Spectra Energy support new devices that make drilling and transporting petroleum easier and safer. Contact us today to learn more about our work within the oil and gas arena.