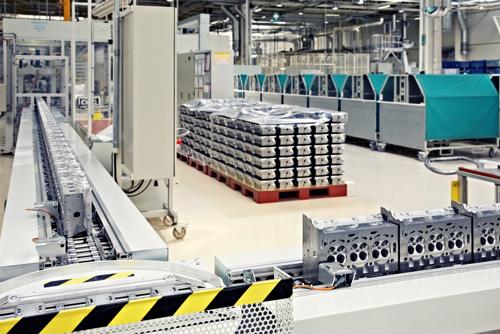
Improving the industrial sector's use of energy with IoT
By Max BurkhalterDecember 14, 2020
In 2019, the industrial sector accounted for 35% of total U.S. end-use energy consumption and 32% of total U.S. energy consumption, according to the U.S. Energy Information Administration, with more than half of that caused by bulk chemical production, refining and mining processes. More than a third of the country's power is eaten up by manufacturing, and even a slight variance in a plant's efficiency can tip this number up or down by millions of dollars annually in energy costs.
Avoiding energy waste is a top priority for plant managers, and the Internet of Things can help. Manufacturers suck enormous amounts of power and require a steady source of fuel to maintain their pace, and waste can be costly. IoT devices can help manage the flow of energy and reduce waste, keeping expenditures closely tied to production values for lowered overhead. When costs go down for energy use, there's more in the budget for expansion and safety measures.
Compliance with guidelines is only the first step; using IoT devices can transform manufacturing and lessen its negative impact on the planet. IoT devices can also help control pollution, with sensors strategically located to alert to the earliest hint of an issue. When monitoring is done scrupulously, and alerts acted on in every case as if it were a true emergency, disasters can be avoided. By not only installing IoT devices and gathering data, but acting on the data in meaningful ways, manufacturers can appeal to consumers who are aware and active about their choice of products.
IoT for optimization
When facility managers can anticipate energy demands, power consumption can be optimized. IoT devices provide a real-time stream of data which can be extrapolated over days, weeks and months to provide a clear picture of the ebb and flow of power demand. Aggregated historical sensor data that has been put through a comprehensive, AI-powered analytics program can provide startling accuracy when it comes to predicting future events. Equipping all HVAC equipment with IoT sensors can evaluate energy usage patterns, and inform future energy consumption to avoid waste, with massive savings available even with tiny percentage changes.
Real-time monitoring also provides opportunities for production teams to anticipate equipment malfunctions. When a piece of equipment can be pulled during scheduled downtime and retrofitted before production starts up again, the impact is orders of magnitude less than when a breakdown on the floor causes an unscheduled halt in production. IoT energy monitoring can also maximize machinery efficiency, and allow machines that need to be warmed up to be started remotely without having staff come in early.
During lulls in production, machines can be turned off, set to idle or kept running with full power loads depending on need and an evaluation of how soon a restart is expected. Finally, equipment that operates around the clock can generate excess heat, wasting energy and causing mechanical issues and a fire risk. IoT sensors can maintain a close watch and sound an alarm if certain heat levels are exceeded.
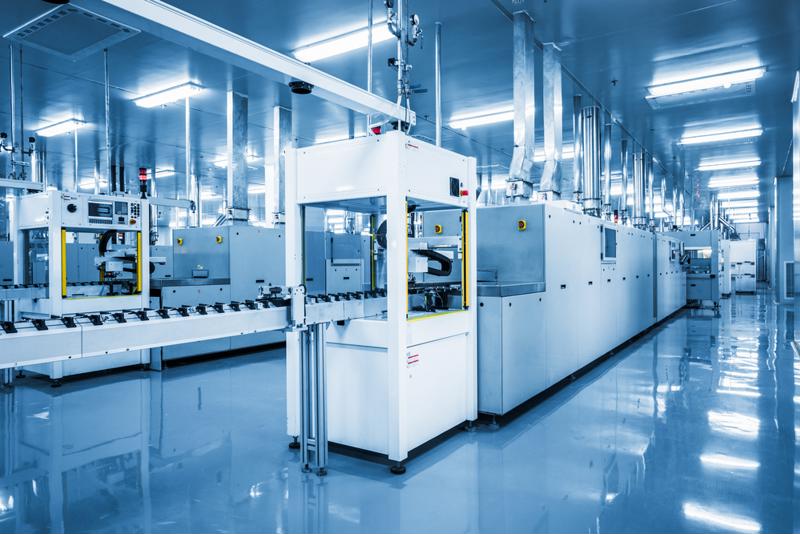
Predictive maintenance
The value of predictive maintenance is a major part of how IoT can reduce overhead. It's not just operational costs that keep production budgets high, but equipment maintenance. Failure to attend to maintenance scrupulously leads to equipment malfunction and hours or days of downtime that eats gigantic holes in the bottom line. To keep shareholders happy with profits, the case can be made for IoT integration that it can generate alerts far enough in advance of a breakdown to safely and seamlessly stop the line, replace the machine and continue without more time wasted than absolutely necessary.
When maintenance requirements are spotted far enough in advance, waiting until the next scheduled break can save even more time and money. By equipping key pieces of production equipment with IoT sensors, manufacturers can monitor the critical production infrastructure, tweak in real time for maximized efficiency and safe parameters of operation, and adapt if something starts to malfunction by lightening the load immediately and planning for a scheduled repair, service, or replacement. The end result is a streamlined effort that takes place on the facility manager and workers' terms, not at the whims of gremlins.
Perle offers high-performance connectivity tools designed to keep industrial manufacturers operating at peak efficiency. Your revenues could increase exponentially as soon as energy waste and potential breakdowns are considered and managed. The IoT can perform wizardry when used correctly, giving you insights into your operation that clarify past events and predict futures ones. Optimize your equipment, facility and IoT connected devices starting today when you contact us for more information.