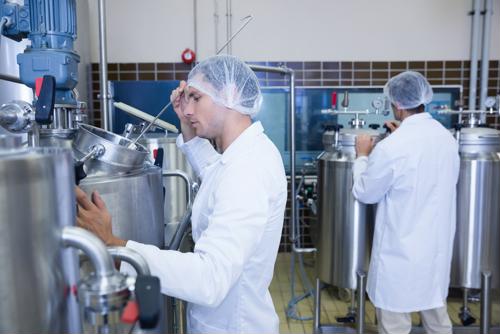
How IoT is transforming U.S. breweries
By Max BurkhalterApril 29, 2019
The internet of things has become a major source of innovation for a wide range of commercial applications, from transportation and package delivery services to large-scale manufacturing procedures. Nearly all production environments and supply chains can benefit from some form of connectivity and automation, but striking the perfect balance between machine-powered operations and human oversight can be difficult. The brewing industry is a great example, as manufacturers of alcoholic beverages utilize complicated multi-step processes that must be precisely monitored and controlled to ensure consistent quality and output. That said, breweries around the world are starting to embrace IoT solutions as a means of increasing their productivity, eliminating waste and crafting better tasting beers.
The internet of beer
The U.S. beer market generated more than $114 billion in 2018, with craft brewers accounting for 24% of all domestic sales, according to the Brewers Association. Craft breweries operate at a much smaller scale than multinational companies like Anheuser-Busch and Heineken, making steady productivity a key driver for their long-term financial success. Integrating IoT-based connectivity tools, such as equipment sensors and data analysis software, offers independent beer makers a streamlined method for refining their brewing conditions and maintaining the health of their machinery.
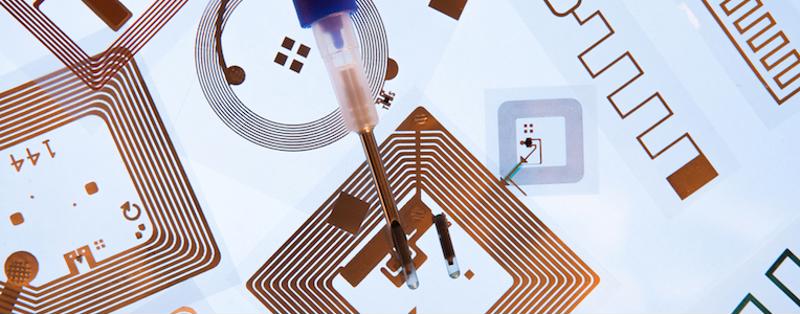
The data generated by embedded technologies allows brewers to keep a close watch on their products during the most volatile steps of the beer making process, including lautering, fermentation and bottling. During these phases, slight variations in temperature and density can have a significant impact on the overall flavor of a beer, making remote monitoring capabilities and automated alerts crucial for maintaining the perfect brewing environment. Waste management is another major concern, as overfilling bottles can lead to costly spills and lost revenue.
"We were losing more than $30,000 a month in beer spillage through the manufacturing process," wrote Joe Vogelbacher, CEO and co-founder of the Sugar Creek Brewing Company, in a blog post on IBM's website. "By integrating new AI and Internet of Things (IoT) technology into our brewing process, we found a solution that supports our commitment to product quality and craftsmanship as well as growing efficiencies."
Some common uses of IoT tech in U.S. breweries include:
- Waste reduction: Outfitting production equipment with embedded flow meters and sensors allows brewers to collect a high volume of accurate data on pressure, temperature, pH balance, carbonation, fill time and more. This can help pinpoint the specific causes of overflow and excessive foaming during the brewing and bottling processes.
- Quality control: Real-time data collection and analysis enables brewers to track each batch of beer through every step of its journey, from pre-production to the shipping bay. This enhanced oversight can help identify irregularities in the brewing process that may negatively impact the quality of the beer.
- Health and safety compliance: Working with large, pressurized containers can pose a significant risk to employees stationed on the production line. Installing pressure sensors on every still, kettle and brewing pump can help production managers track any performance issues that could lead to a serious accident.
Perle offers high-performance networking tools that can help breweries operate with maximum efficiency and oversight. Read some of our customer stories to find out how we've helped other companies take full advantage of IoT solutions.