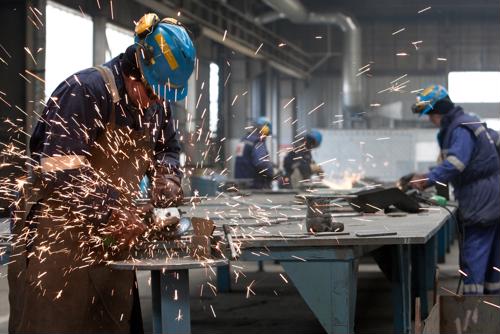
How IoT devices are improving workplace safety
By Max BurkhalterMarch 18, 2019
The internet of things has helped companies across a variety of industries streamline their operations and increase productivity, but real-time data collection and reporting also have the potential to improve working conditions for employees all over the world. According to the National Safety Council, work-related injuries that required medical consultations totaled 4.5 million in 2017, which cost an estimated $161.5 billion in medical expenses, wage and productivity losses, administrative expenses and more. Workers in the construction, manufacturing and agricultural industries encountered some of the highest numbers of injuries and deaths, though workplace safety has continued to improve as new technologies become more affordable and easy to implement.
While IoT devices cannot completely shield workers in high risk industries from every category of hazard, they are helping facility and worksite managers address a large number of preventable threats. In a recent article published by IoT For All, guest writer Bryan Christiansen, founder and CEO of Limble CMMS, pointed to five converging technologies that can process and identify workplace trends with greater accuracy, including:
- Deep dive analytics
- Artificial intelligence
- Cloud storage
- Big data processing
- Interconnected devices
Together, these technologies are able to aggregate a massive amount of environmental data that may lead to actionable solutions for some of the most common workplace hazards, such as high temperatures, oppressive humidity, excessive noise levels and unhealthy air quality. To get an idea of how IoT tech is revolutionizing workplace safety, consider these interesting implementation examples:
Wearable IoT
Workwear manufacturers have been championing the value of IoT-enabled clothing for some time, as it allows facility managers to keep an eye on their employees' vitals as they go about their work. For example, industrial manufacturing companies have begun outfitting their workers with heart monitors to help them identify signs of overexertion and prevent any health-related consequences that may ensue. These tools are extremely useful in harsh working environments — like factories, energy production facilities, construction sites and warehouses — where production teams and maintenance crews spend most of their time in close proximity to potentially dangerous machinery and equipment.
In 2018, Digitalist Magazine spotlighted a U.S. device manufacturer that has been working to develop the next generation of wearable communication systems. The startup company, named Heads Up, created a compact IoT device that is able to detect "out-of-tolerance conditions for heat, humidity, and noise levels." The device can be easily affixed to an eyepiece and will flash different colored lights to alert the wearer of harmful changes in the surrounding environment. This tool can not only help workers limit their exposure to dangerous working conditions, but it can also connect to enterprise data systems and back-end analysis engines to support future safety initiatives.
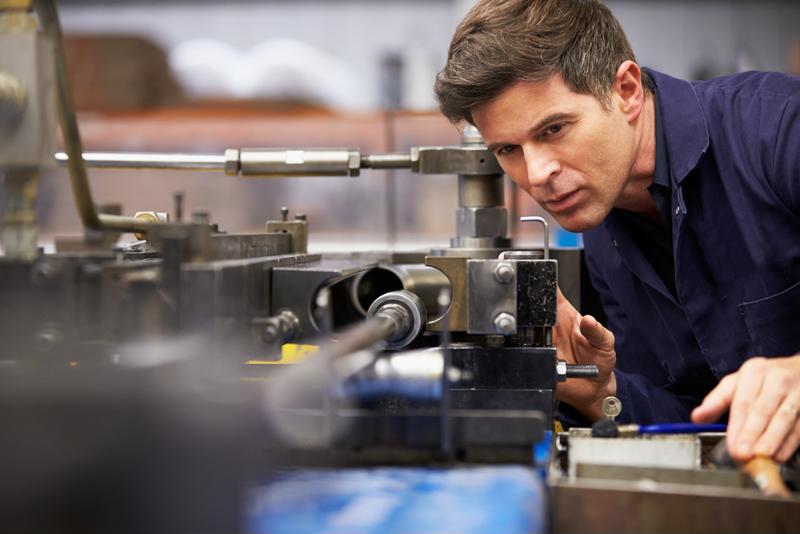
Predictive equipment maintenance
All industrial machinery requires routine maintenance and repairs over the course of its operational lifespan, but it's not always obvious when a piece of equipment needs to be worked on. Employees operating these powerful machines face a variety of risks if an internal component were to fail unexpectedly, or if a safety feature were to malfunction during a maintenance project. Preventing large-scale accidents has always been a major concern for production and manufacturing facilities, which has lead some companies to embrace a time-based maintenance schedule. While this strategy has helped to reduce serious and unexpected breakdowns, it can also result in the replacement of machine components that have not yet worn out, costing thousands in the long run.
According to an article published by Automation World in early March, many of the leading automation vendors have started embedding improved safety and monitoring features into their core systems, rather than rolling them out during the post-production phase. By incorporating passive safety measures into their equipment machine logic, equipment manufacturers are hoping to support predictive maintenance strategies that allow for less downtime without jeopardizing the wellbeing of equipment operators. For example, Endress+Hauser Management produces smart instrumentation that can control the pressure and temperature of liquids flowing through piping without direct human intervention. Moving forward, workplace safety will increasingly depend on a company's willingness to invest in cutting-edge data collection and reporting technologies
Why scalable IoT infrastructure is key
As IoT technology continues to improve, facility and worksite managers will be able to deploy a host of safety-focused devices that will keep workers informed about the exact conditions of their production equipment, along with any hazards that may be present. But before industrial players can start leveraging these devices en masse, they must first ensure their networking infrastructures have the bandwidth capabilities to process all the generated data. Taking full advantage of cloud computing, big data analytics and IoT-enabled devices relies flexible communication tools that can be expanded without the need for a complete system overhaul.
Perle offers powerful connectivity tools that can help facility managers maintain efficiency during the rollout of new safety equipment, such as our industrial-grade ethernet switches and robust console servers. Read some of our customer stories to find out how we've empowered other forward-thinking companies in their quest to create a safer working environment for their employees.