
How IIoT vibration sensors improve factory uptime
By Max BurkhalterMarch 6, 2019
The industrial internet of things has continued to evolve at a blistering pace, spurred on by new technologies that allow manufacturers to collect and analyze massive quantities of production data. The insights generated from these technologies have helped to revolutionize how workflow managers monitor their equipment and structure their operational environments, leading to huge gains in efficiency and a reduction in maintenance costs. IIoT sensors are at the forefront of this manufacturing innovation, as they enable real-time reporting of equipment health and production output without interrupting the supply chain.
While IIoT modernization was slow at first, manufacturers around the world have started embracing the transformative power of machine learning and big data connectivity. According to a study from Transparency Market Research, the global IIoT market is expected to expand at a compound annual growth rate of 24.3 percent over the next seven years, reaching an estimated $991,562 million by 2026. This massive expansion is, in part, a reflection of the broader shift toward industrial automation and machine-to-machine communication systems, which hold the potential to significantly increase operational efficiency and productivity.
VocalZoom unveils new vibration sensors
In early March, VocalZoom announced the release of its newest vibration sensing technology, specifically designed for monitoring fast-paced IIoT manufacturing environments. Unlike traditional sensors - which are often based on a combination of micro-electro-mechanical, piezoelectric and acoustic technologies - VocalZoom's non-contact tech is able to accurately measure the vibrations emitted by both new and old machinery. This allows manufacturers to monitor a wider array of equipment and use cases without the standard production downtime and deployment costs that most sensors require during installation, as reported by IoT Evolution World.
One issue with direct-contact IIoT sensors is the difficulty of affixing them to legacy manufacturing equipment, as older machinery was not designed to accommodate external monitoring devices. Since most manufacturers rely on established machinery in their day-to-day operations, using traditional sensors could disrupt their production line or feed inaccurate information to their reporting software. Additionally, these sensors may not be able to fully integrate with equipment that contains several moving parts or operates at a high temperature, preventing facility managers from capturing a complete picture of the health and functionality of their machinery.
To address these limitations, VocalZoom designed industrial sensors that use the self-mixing interference effect of laser diodes to measure the exact vibrations, distance and velocity of a machine without the need for direct contact. In fact, VocalZoom's sensors can track subtle vibrations from up to 3 meters away, making them incredibly easy to install and operate, regardless of the tough environmental conditions they're used within. This monitoring solution holds the potential to completely revolutionize manufacturing environments, as the lack of direct contact reduces the sensor's exposure to potentially corrosive elements, thereby increasing its operational lifespan.
"The Industrial IoT is only as good as the sensors that monitor machine performance," said Tal Bakish, CEO of VocalZoom, as cited by IoT Evolution World. "Unfortunately, most IIoT sensors are built on technology that makes predictive maintenance solutions expensive and unreliable for a number of important use cases. Our vibration sensors represent the next generation of predictive maintenance solutions, offering better monitoring at lower cost for up to 70 percent of all industrial machinery."
VocalZoom's vibration sensors come with a wide range of tangible benefits, including improved accuracy, minimal downtime during installation and maintenance, and increased coverage for complex machinery. The sensors are immune to ambient noise (a major limiting factor for audio-based sensors) and do not require batteries. While the sensors have already hit the market, it may take some time before manufacturing professionals have a beat on the technology's weaknesses.
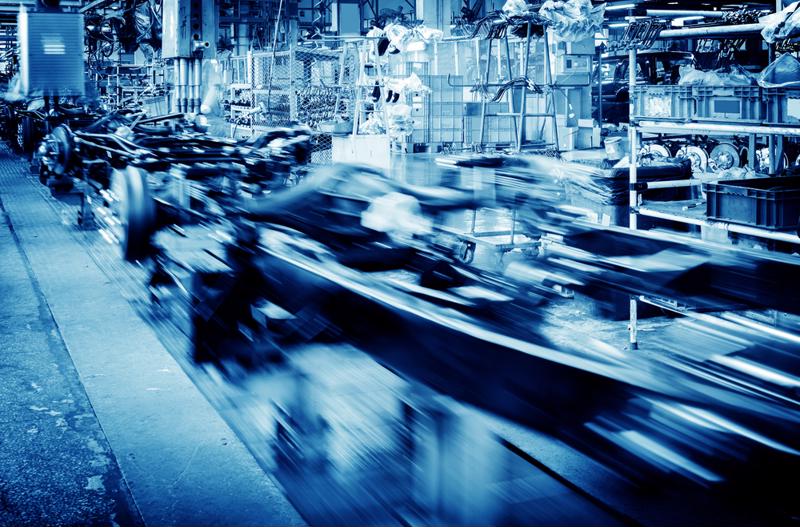
The value of predictive maintenance
IIoT innovation has opened up new possibilities for reducing maintenance costs and equipment breakdowns through data collection and remote monitoring software. Industrial machinery outfitted with vibration sensors can provide facility managers with a constant stream of real-time information about the equipment's performance and operational condition. If a piece of machinery experiences an unplanned slow down or service interruption, a detailed health report is generated and sent to the appropriate maintenance team. Rather than waiting around for something to break, industrial manufacturers can schedule repairs and replacements before their equipment actually malfunctions, which in turn extends the operational life of their production environment.
However, aggregating the massive amount of data generated by an entire fleet of vibration sensors requires a stable network and a lot of bandwidth. That's why it's important for facility managers to assess the networking capabilities of their production line before investing in a new IIoT system, as failing to do so can leave them vulnerable to frequent connectivity problems and network outages.
Perle offers powerful networking tools that can help increase production efficiency and facilitate stable data networks, like our industrial-grade ethernet switches and robust console servers. Read some of our customer stories to find out how we've empowered other manufacturing companies in their quest to optimize operations and secure a more productive workflow.