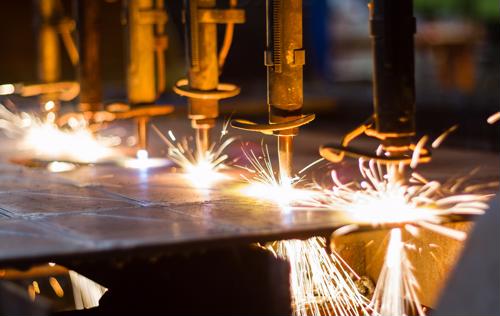
How IIoT could save manufacturers millions in overhead costs
By Max BurkhalterOctober 25, 2019
The introduction of the industrial internet of things and connected technologies has opened up a new frontier for manufacturing companies. With Industry 4.0 in full swing, manufacturers across the U.S. are taking every opportunity to optimize their operations, reduce waste and increase their bottom line. Of course, integrating IIoT into large-scale production environments often requires considerable hardware, software and cybersecurity investments, leading some companies to take a slow-roll approach. While this caution is certainly justified, opting out of modernization altogether could prevent manufacturers from significantly reducing their energy consumption and equipment maintenance costs.
Although commercial IIoT tech is a relatively new innovation, it's already having a profound effect on how manufacturers structure, manage and improve their production lines. For one, the presence of wired and wireless sensors provides enhanced visibility over environmental conditions, equipment performance and more. The massive amount of real-time data generated by these IIoT sensors can be leveraged to, among other things, develop more efficient processes for manufacturing goods. But to understand the potential economic impact of large-scale IIoT adoption, it may be useful to take a closer look at the specifics.
Improving energy efficiency with IIoT
First, it's important to note that manufacturing companies and other industrial sector organizations accounted for around 32% of total U.S. energy consumption in 2018, according to the U.S. Energy Information Administration. In most cases, the electricity used to power industrial operations was supplied by utility companies or independent power producers, which often had a direct impact on the national power grid. Manufacturers heavily rely on a steady supply of energy to generate heat for industrial processes, power their heavy machinery and keep their facilities warm and well-lit. As such, a lapse in supply can have serious repercussions for the general sustainability of their production lines, which may encourage companies to draw more power than they need.
Generally speaking, IIoT can help solve this dilemma by providing facility managers with the ability to anticipate energy demands and optimize their power consumption with increased precision. This is typically achieved by aggregating a massive volume of historical sensor data and running the information through a predictive analytics program. For example, equipping all heating, ventilation and air conditioning equipment with IIoT sensors could help manufacturers identify energy usage patterns that can be acted upon, along with any sources of energy waste. Considering HVAC systems are major contributors to energy consumption in nearly all industrial settings, even minor improvements could have positive economic repercussions. In fact, one study conducted by the McKinsey Global Institute found that IIoT could help manufacturers save up to 20% in energy costs.
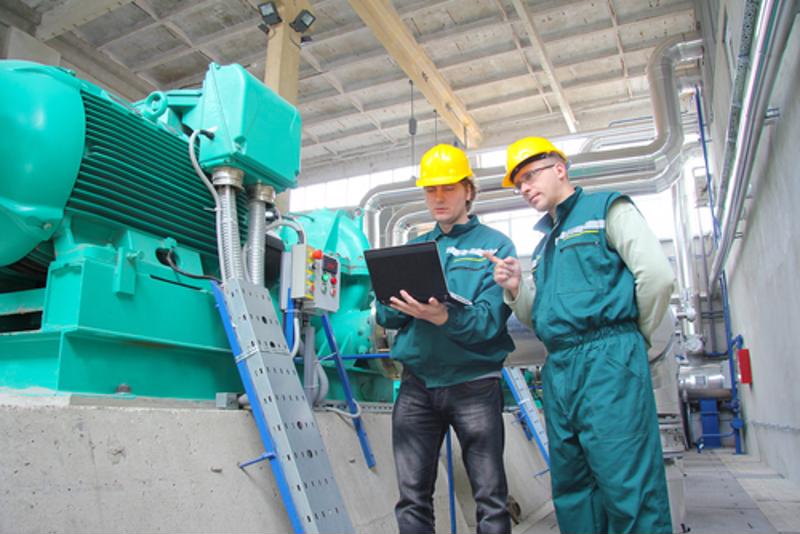
Another major benefit of IIoT energy monitoring is that it allows facility managers to maximize the efficiency of their production machinery. Knowing when certain equipment should be powered on and fully operational can help reduce consumption and conserve electricity during lulls in production. As pointed out by a recent article from Supply Chain Digital, keeping equipment operating around the clock can lead to excess heat, which is often an indicator of energy waste and/or a mechanical issue. Addressing these and other power consumption challenges will likely require a good deal of operational planning and experimentation on the part of manufacturers, but the long-term results could be well worth the upfront investment.
IIoT and the value of predictive maintenance
Equipment maintenance is yet another source of high overhead costs for today's manufacturers, especially when you consider the monetary impact of unexpected downtime. According to a recent study by Accruent, unplanned downtime costs industrial manufacturing firms close to $50 billion every year, with each incident ranging from $10,000 to $250,000 per hour of inoperability. While these estimates do incorporate labor and material costs along with projected productivity losses, the true impact of faulty machinery can be difficult to pin down. However, by outfitting production equipment with IIoT sensors, manufacturers can monitor the health and performance of critical infrastructure in real-time and make adjustments whenever necessary.
What makes IIoT so valuable for the manufacturing sector is that it allows companies to combine big data with human insight to help improve overall decision making. For example, environmental sensors are able to detect when a piece of machinery is running at higher-than-normal ambient temperatures and send an alert to the asset management team. Once notified, these professionals can sift through the historical data and make a more informed determination about the cause of the problem. This predictive approach to maintenance allows companies to address performance issues before they turn into large-scale repair jobs, leading to a potential net saving of $240 and $630 billion globally by 2025, according to the McKinsey Global Institute. But before manufacturers can take full advantage of IIoT tech, they must first ensure their networking and connectivity hardware is scalable and secure.
Perle offers high-performance connectivity tools that can keep manufacturers operating at peak efficiency, from robust Terminal Servers and Industrial Switches to reliable Fiber Extenders and Media Converters. Read some of our customer stories to find out how we've helped other organizations optimize their IIoT systems for the future of manufacturing.