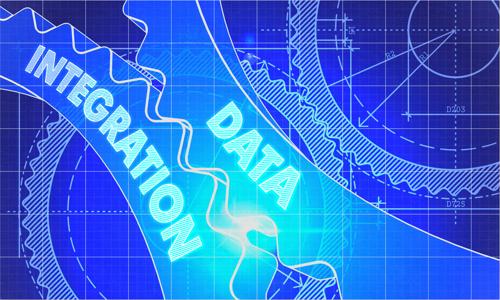
Digital tools transforming industry - Is your network ready?
By Max BurkhalterSeptember 22, 2016
Digital technologies are changing process industries. Organizations have an opportunity to use Internet of Things technologies along with more traditional solutions, such as enterprise resource planning platforms, to bring data together from diverse sources and use it to inform everyday operations. The potential benefits here can be substantial, but all of these gains can only be achieved if companies have network infrastructure in place to move data between disparate systems. This transition is a key motivating factor behind increased industrial Ethernet investments, and organizations that make strategic technology choices can now position themselves ideally for the future.
"Businesses are expected to spend $907 billion annually on Industry 4.0 technologies through 2020."
Considering the potential of Industry 4.0
The idea of a new industrial revolution - known as Industry 4.0 - reflects the potential transformation offered if organizations are able combine the IoT with advanced networking tools, software and apps that allow them to digitize and streamline operations. A recent Pricewaterhousecoopers study found businesses are expected to spend approximately $907 billion annually on Industry 4.0 technologies through 2020. This is a great deal of money, but companies are also expected to glean 3.6 percent cost savings annually over the next five years. Furthermore, organizations anticipate achieving revenue gains of 2.9 percent from effective digitization.
All told, the costs of updating operations in response to Industry 4.0 may be substantial, but the gains are significant enough to justify the costs. PwC totaled the projected revenue increases and cost reductions businesses are expecting:, and the figure came to $914 billion annually. If organizations, on the whole, are spending $907 billion, that's a global economic ROI of $7 billion from investments in Industry 4.0 solutions.
All of these benefits sound exciting, and there are plenty of respondents to the PwC study that expect significant results from Industry 4.0:
- Approximately 35 percent said they expect revenue gains will exceed 20 percent during the next five years.
- Another 43 percent believe annual cost savings will be greater than 20 percent.
Industry 4.0 provides organizations with an opportunity to digitize their operations and glean all the benefits that come with innovation, and McKinsey found many businesses have high expectations when it comes to digital processes.
Unpacking specific benefits of Industry 4.0
From a big-picture perspective, Industry 4.0 has the potential to combine with additive manufacturing, sophisticated robotics solutions and similar advances to transform operations to drive better customer experiences. These technologies are coming together to change the way manufacturers operate, and respondents to McKinsey's survey expect the emerging tools to impact a wide range of functions, including:
- Reducing maintenance costs - Respondents expect reductions of between 20 and 40 percent as the ability to gather data from diverse sources enables manufacturers to employ capabilities like predictive maintenance with greater precision.
- Time to market - The ability to quickly move information between various sources combines with options like additive manufacturing to make it easier to get new solutions out to market, and respondents expect reduction in the time to market to reach between 20 and 50 percent.
- Better forecasting - Access to data from a wide range of sources increases the precision with which organizations can make predictions, and individuals polled by McKinsey expect, on average, to have forecasting accuracy increase to greater than 85 percent.
The benefits of digitization within an Industry 4.0 environment - be they cost gains mentioned by PwC or operational advantages the operational advantages noted by McKinsey, can only be achieved if manufacturers have the infrastructure they need to move data between all areas of operations.
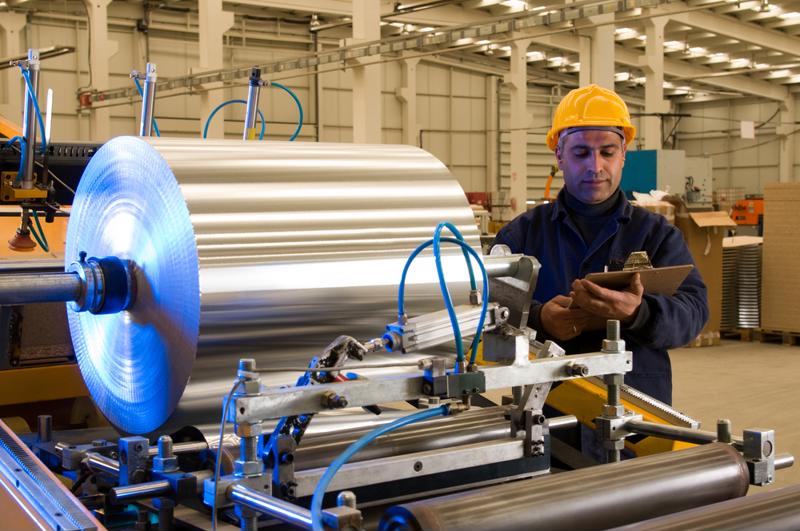
Digital technologies are transforming the manufacturing sector.
Overcoming the networking divide
Industrial networks are traditionally heavily segregated, with a wide range of protocols being put into use for specific functions. For a long time, separating these networks was necessary because Ethernet couldn't handle the specific performance or environmental demands that different industrial workflows present. This has begun to change as Ethernet has evolved substantially in recent years, and the combination of better Ethernet and new operational demands has made completing a network overhaul important for a wide array of industrial organizations. Modern industrial Ethernet technologies can:
- Withstand extreme operating environments.
- Ensure lossless data transmission to support data transit in automation and control networks.
- Interconnect every facet of operations on a common network to streamline data transit.
Imagine a customer logs onto your website and requests a customized version of one of your products. How does your sales team get that information? How dos the request go into your warehouse and production systems? Traditionally, this communication and coordination required manual data management and communication. Digitizing operations around Industry 4.0 technologies and procedures keeps those disparate areas of operations unified. This extends beyond moving data and out to making sure users get the information they need to enact procedures like just-in-time inventory management and robust predictive maintenance procedures. Industry 4.0 offers significant gains, and the network can make those benefits possible.
Perle has over 516 models of Managed Industrial Ethernet Switches with the vast array of options including 10/100/1000 Ethernet, PoE, fiber and combo ports. Perle IDS Industrial-grade Ethernet Switches are ideal for the harsh environments found in industrial factory systems and outdoor applications.