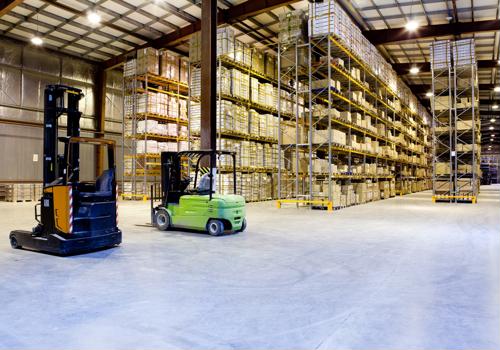
Automating your warehouse: Where to start
By Max BurkhalterApril 8, 2021
Automating your warehouse can allow you to scale effortlessly without increasing employee headcount or letting anyone go. It's a perfect solution for reducing costs and improving productivity. In many cases, resistance against automation is driven by fears that human workers will lose their jobs, but this is rarely the case. Technology makes warehouse processes more efficient by automating tedious, manual tasks, augmenting the work of humans and freeing them up to focus on more challenging, complex tasks.
Warehouse automation can allow a company to enter and maintain a growth stage without the need to hire more staff. Robots and other machines provide a high level of accuracy, as well as an ability to work continuously without being subjected to labor laws or fatigue experienced by human workers. All of this means that automation can make warehouse tasks safer and more efficient
Types of warehouse automation
According to 6 River Systems, there are many separate and distinct types of warehouse automation, although multiple technologies can be pulled together under one roof.
Goods-to-person (GTP) can mean that machines or robots fetch materials to workers for assembly or packing. The earliest form of this technology was conveyer belts followed by carousels. Today, automated storage and retrieval solutions (AS/RS) such as autonomous vehicles and mobile cranes can move around a warehouse, storing items or accurately picking products and delivering them to assembly or packing stations manned by humans. Sortation systems are designed to identify and separate items correctly, sending them off to the appropriate warehouse location. These are useful when unpacking new shipments or handling returns.
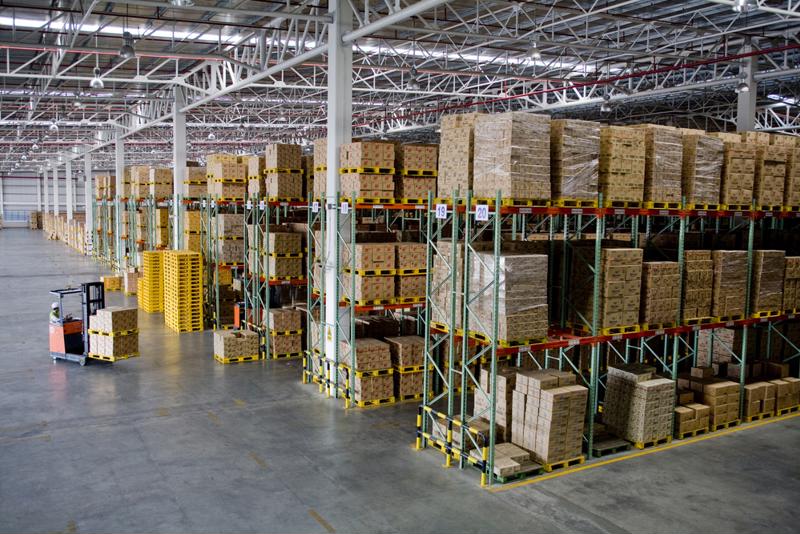
Pick-to-light systems use barcodes and LED lights to show human workers the exact location of desired items to fulfill orders, cutting down on walking and searching to find the correct products and improving productivity via faster item locating. Voice picking and voice tasking solutions add a layer of communication technology to warehouse order picker routines, allowing taskers and pickers to effortlessly coordinate movement and picking tasks for faster, more efficient processes.
Collaborative mobile robots (cobots) enable higher efficiency by working alongside humans, and can optimize picking routes and tasks based on work priorities and warehouse status. Drones are simpler than cobots, lacking the highly sophisticated onboard computers, and are more likely to be deployed with bar code scanners to complete inventory counts. Warehouse drones can alert staff to items that have been stored in an incorrect location, or which require restocking.
Benefits of warehouse automation
According to CamCode, there are dozens of ways in which warehouse automation can benefit your organisation.
Benefits of warehouse automation include increased productivity and accuracy; fewer injuries and less worker stress, strain, and fatigue; higher levels of worker satisfaction, since employees can be directed to more rewarding tasks; reduced operating costs; and fewer picking and shipping mistakes. Space can be optimized and maximized since items can be stored far above worker reach and or below waist-level without requiring workers to climb or stoop. Forklifts can be replaced with slimmer, space-saving cranes and transport vehicles that run autonomously and can maneuver in tighter spaces.
Investing in the right warehouse automation solutions is a smart decision, and so is investing in base technologies to connect your warehouse to your internal systems and supply chain. Perle can help you implement the latest in industrial Ethernet and other tech to keep your warehouse operations running smoothly. Read our customer success stories today.