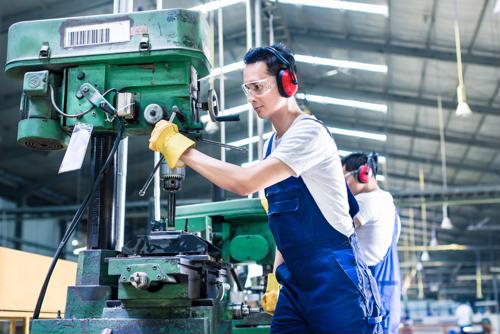
5 ways to keep the factory network safe from a breach
By Donna DonnowitzJanuary 27, 2016
Owners and executives in the industrial and manufacturing sectors may not think of their businesses as likely marks for cybercriminals, but this is a major misconception. In fact, government officials have recently identified industrial control systems as one of the most important emerging targets for cybercriminals in 2015, according to Reuters. If hackers have already found ways to monetize breaches into financial and health care systems, then it's only a matter of time before other industries see similar frequencies of cyberattacks. The industrial sector seems to be next on the list, so the pressure is on decision-makers in manufacturing to ensure that their factory network remains secure in 2016.
1. Enhance physical security with new company policy
Most managers aren't accustomed to treating the factory floor like a data center, but the digitization of the manufacturing process has changed the stakes. Physical security of network gear and connected devices has become a necessity.
One of the most efficient ways to address this vulnerability is through changes in policy. Taking steps to increase transparency and accountability in manufacturing environments will have a big impact on influencing company culture to treat the entire factory. Greater involvement from the C-suite, either in the form of allocated resources or a newly announced company initiative, will encourage employees to implement these changes as quickly as possible.
2. Deploy white hat professionals to find weaknesses
Sometimes the only way to beat cybercriminals is to get inside their heads. While companies may not have an infiltration expert on hand to test their systems, Entrepreneur pointed out that more companies are relying on white hat hackers to address this very problem. These code experts are familiar with the tools and tricks that hackers use to get around a company's digital defenses, and offer their services to companies that desire to see how well their best practices stand up to a targeted hacking effort. This strategy may end up creating new costs when holes in security are discovered, but these costs will still seem minimal in comparison to the consequences of a major security breach.
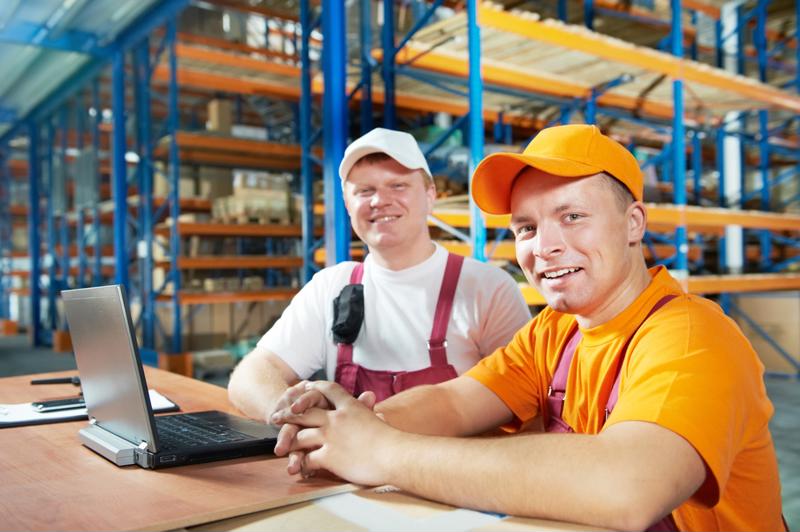
Any piece of equipment connected to the network becomes a possible target for hackers.
3. Manage data transfers between company networks
Factory floor networks are often modeled and assembled separately from one another. That's why it's no surprise that connectivity and security are compromised when data moves from one system to the next. Unless tech professionals in the manufacturing sector are able to crib together a secure, interconnected network from the start, there's a good chance that steps must be taken to make the factory floor a less inviting target for cybercriminals.
Companies can take a straightforward approach to solving this problem by investing in secure network gear like high-performance Ethernet switches. These network devices provide adopters with the encryption necessary to keep enterprise data safe from prying eyes. Manufacturing Business and Technology pointed out that this attention to detail is especially important when company networks are organized into a hierarchy of trust.
4. Stop treating anomalies like isolated incidents
Another way that factory managers can limit vulnerabilities in the factory network is by paying closer attention to anomalous reports or hiccups in production. Cybercriminals typically spend several weeks monitoring targeted servers and identifying opportunities to leverage their intrusions for a big payoff. In this modern era of connected devices, mysterious equipment failures could be evidence of a hacker testing their hold over the factory network. Decision-makers in the manufacturing sector must also account for the possibility that their network has already been compromised.
"Account for the possibility that the network has already been compromised."
5. Limit cloud storage to corporate applications
Cloud storage is a vital resource for manufacturers of all sizes, but security and reliability problems inherent to third-party storage can limit the cloud's usefulness. This is the case with pertinent manufacturing and enterprise data collected by manufacturers from the factory floor. Keeping this data on-site via traditional storage and backup technology ensures that critical pieces of information are always close at hand.
Third-party storage providers charge customers a hefty premium for data security, but major hacks in 2014 and 2015 demonstrated that no network is safe. Factory managers are often better off keeping digital assets nearby rather than rolling the dice on the cloud.
Perle has over 516 models of Managed Industrial Ethernet Switches with the vast array of options including 10/100/1000 Ethernet, PoE, fiber and combo ports. Perle IDS Industrial-grade Ethernet Switches are ideal for the harsh environments found in industrial factory systems and outdoor applications.